5 Warning Signs Your Accessibility Lift Needs Servicing
Introduction
Accessibility lifts are essential for providing mobility solutions to people with disabilities, ensuring everyone can move freely and safely. Regular maintenance of these lifts is crucial, but sometimes it can be challenging to know when servicing is needed. Here are five warning signs that your accessibility lift might require professional attention.
Unusual Noises
One of the first signs that your accessibility lift needs servicing is the presence of strange or unusual noises. If you start hearing grinding, squeaking, or banging sounds during operation, this could indicate issues with the lift's components, such as the motor or gears. Ignoring these sounds can lead to more severe problems.
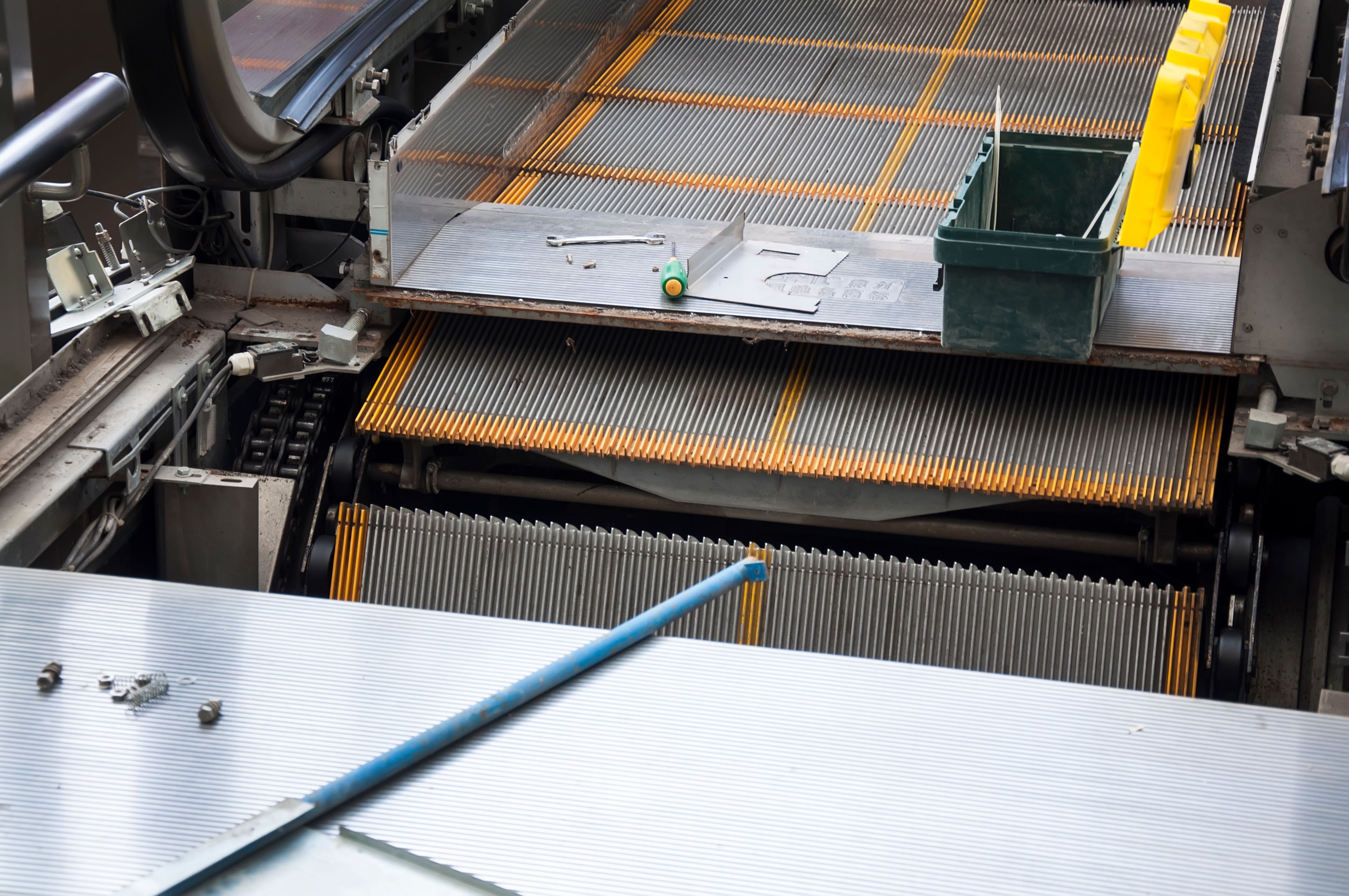
What to Do
It's essential to address these noises promptly by consulting a professional technician who can diagnose and fix the problem. Regular lubrication and inspection can often prevent these issues from arising in the first place.
Slow Movement
If your lift is moving slower than usual or seems to struggle when lifting or lowering, it's a clear sign that servicing is needed. Reduced speed can be caused by various factors including motor issues, electrical faults, or even obstructions on the track.
Potential Causes
- Worn-out motor components
- Electrical wiring problems
- Lack of proper maintenance
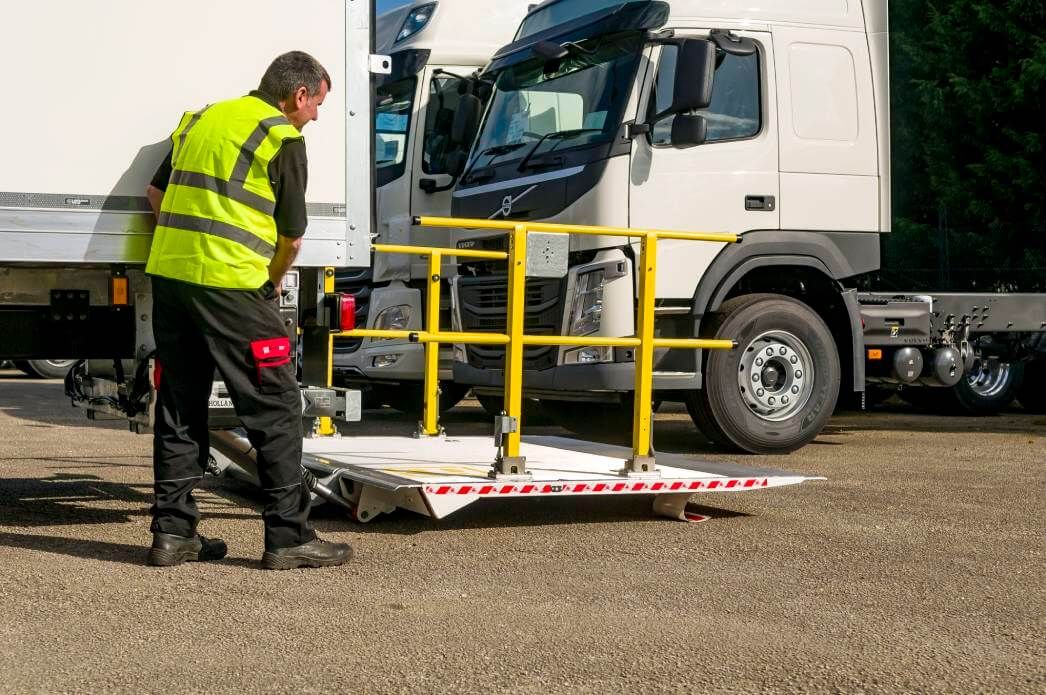
Frequent Breakdowns
Experiencing frequent breakdowns or malfunctions with your accessibility lift is a major red flag. If your lift stops working unexpectedly or requires frequent resets, this could indicate underlying mechanical or electrical problems that need immediate attention.
Preventive Measures
To avoid frequent breakdowns, ensure that your lift undergoes regular maintenance checks and servicing. This will help in identifying potential issues before they become significant problems.
Visible Wear and Tear
Inspect your lift regularly for any visible signs of wear and tear. This includes frayed cables, cracked panels, or loose components. Such physical damage can compromise the safety and functionality of the lift.
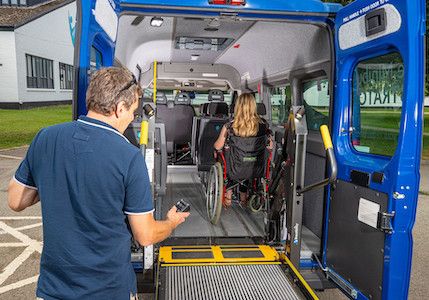
Maintenance Tips
Address visible wear and tear by scheduling routine inspections and repairing or replacing damaged parts promptly. This proactive approach will ensure the longevity and safety of your lift.
Unresponsive Controls
If the controls of your accessibility lift become unresponsive or delay in responding, this could be an indication of electrical issues or a failing control system. Consistent responsiveness is crucial for safe operation.
Steps to Take
When facing unresponsive controls, seek immediate professional assistance to troubleshoot and resolve the issue. Regular testing of control systems during maintenance checks can help in early detection of such problems.
Conclusion
Ensuring that your accessibility lift remains in optimal condition is essential for the safety and convenience of its users. By paying attention to these warning signs and scheduling regular maintenance, you can prevent costly repairs and ensure reliable performance. Remember, proactive care is always better than reactive measures when it comes to accessibility equipment.