Understanding Regulations for Vehicle Lifts in Lincolnshire
Introduction to Vehicle Lift Regulations
In Lincolnshire, as in the rest of the UK, vehicle lifts are essential for a wide range of automotive services. From routine maintenance to complex repairs, these lifts ensure that work can be conducted safely and efficiently. However, with their use comes the responsibility of adhering to specific regulations designed to protect both the operator and the vehicle. Understanding these regulations is crucial for any business involved in automotive services.
The Health and Safety Executive (HSE) outlines several key regulations that businesses must follow. These guidelines are aimed at reducing the risk of accidents and ensuring that all equipment is maintained correctly. For businesses in Lincolnshire, complying with these regulations is not just a legal obligation but also a commitment to safety.
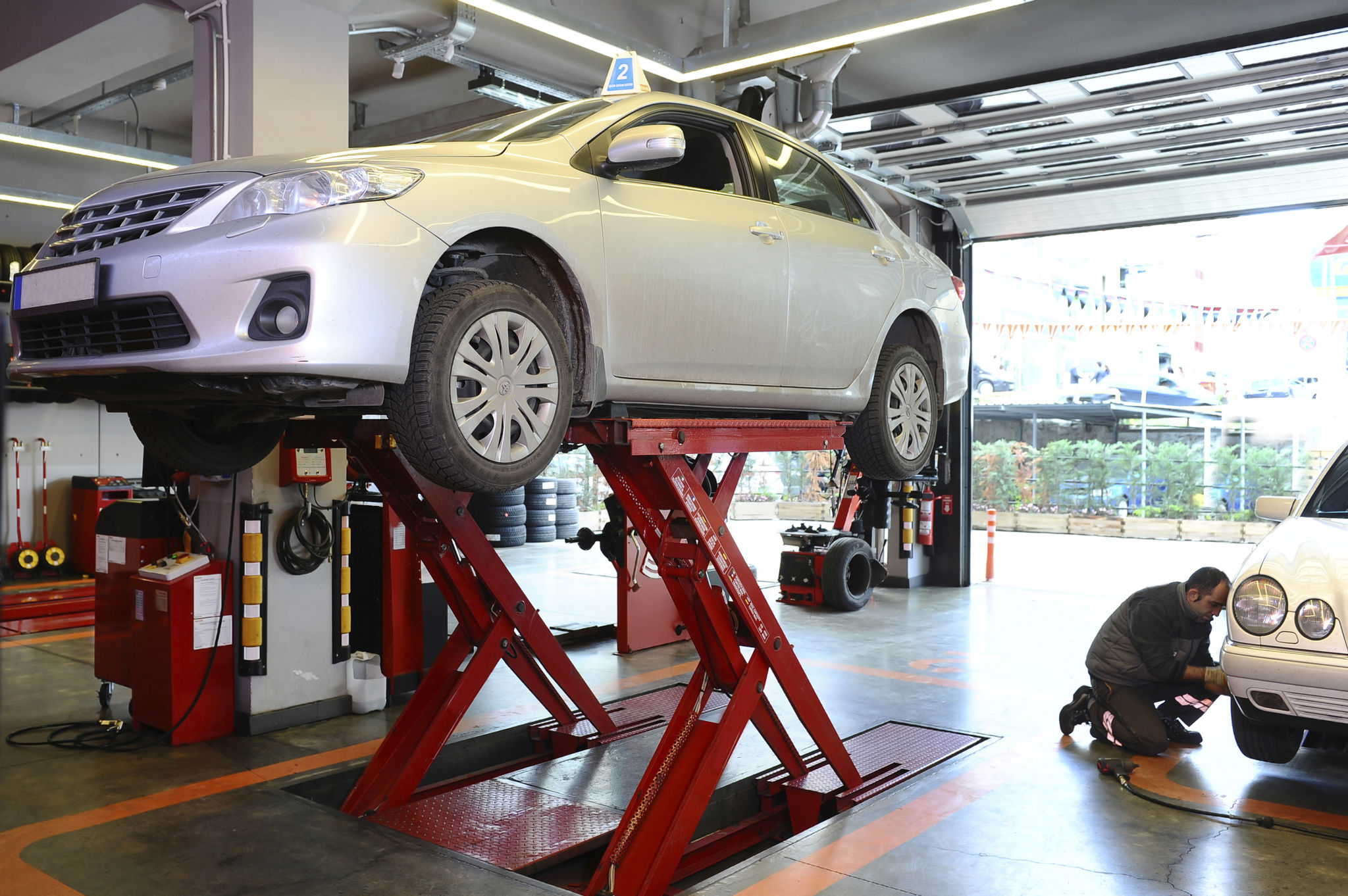
Key Regulations to Consider
The main regulations governing vehicle lifts in Lincolnshire include the Provision and Use of Work Equipment Regulations 1998 (PUWER) and the Lifting Operations and Lifting Equipment Regulations 1998 (LOLER). These laws require that all equipment used in lifting operations is suitable for its intended purpose, properly maintained, and inspected regularly by a competent person.
Provision and Use of Work Equipment Regulations (PUWER)
PUWER requires employers to ensure that work equipment is suitable for its intended use, safe for use, and maintained in a safe condition. It also mandates that employees using the equipment have received adequate training. This regulation applies to any business using vehicle lifts, from large dealerships to small independent garages.
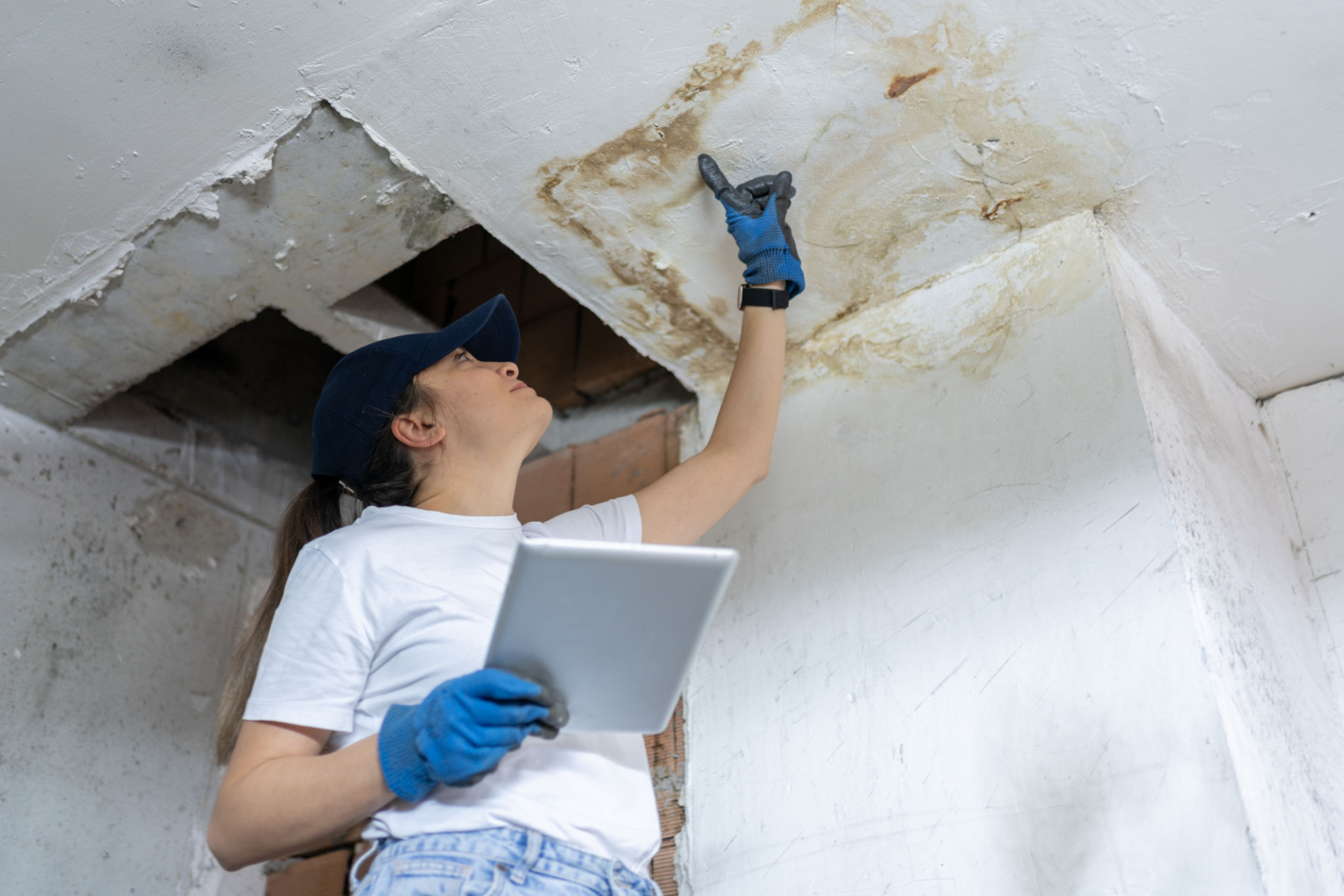
Lifting Operations and Lifting Equipment Regulations (LOLER)
LOLER focuses specifically on the lifting operations themselves. It requires that all lifting equipment is positioned or installed to prevent the risk of injury and that lifting operations are properly planned, supervised, and carried out by competent people. Regular inspections and maintenance are key components of LOLER compliance.
Inspection and Maintenance Requirements
Regular inspections are a critical part of maintaining compliance with both PUWER and LOLER. Vehicle lifts should be inspected at least every six months or more frequently if they are used heavily or in harsh conditions. These inspections should be conducted by a qualified engineer who can identify potential issues before they become serious problems.
Maintenance should follow the manufacturer's guidelines and include regular checks for wear and tear, as well as testing of safety features such as locking mechanisms and emergency stop buttons. Keeping detailed records of all inspections and maintenance activities is not only a good practice but also a requirement under these regulations.
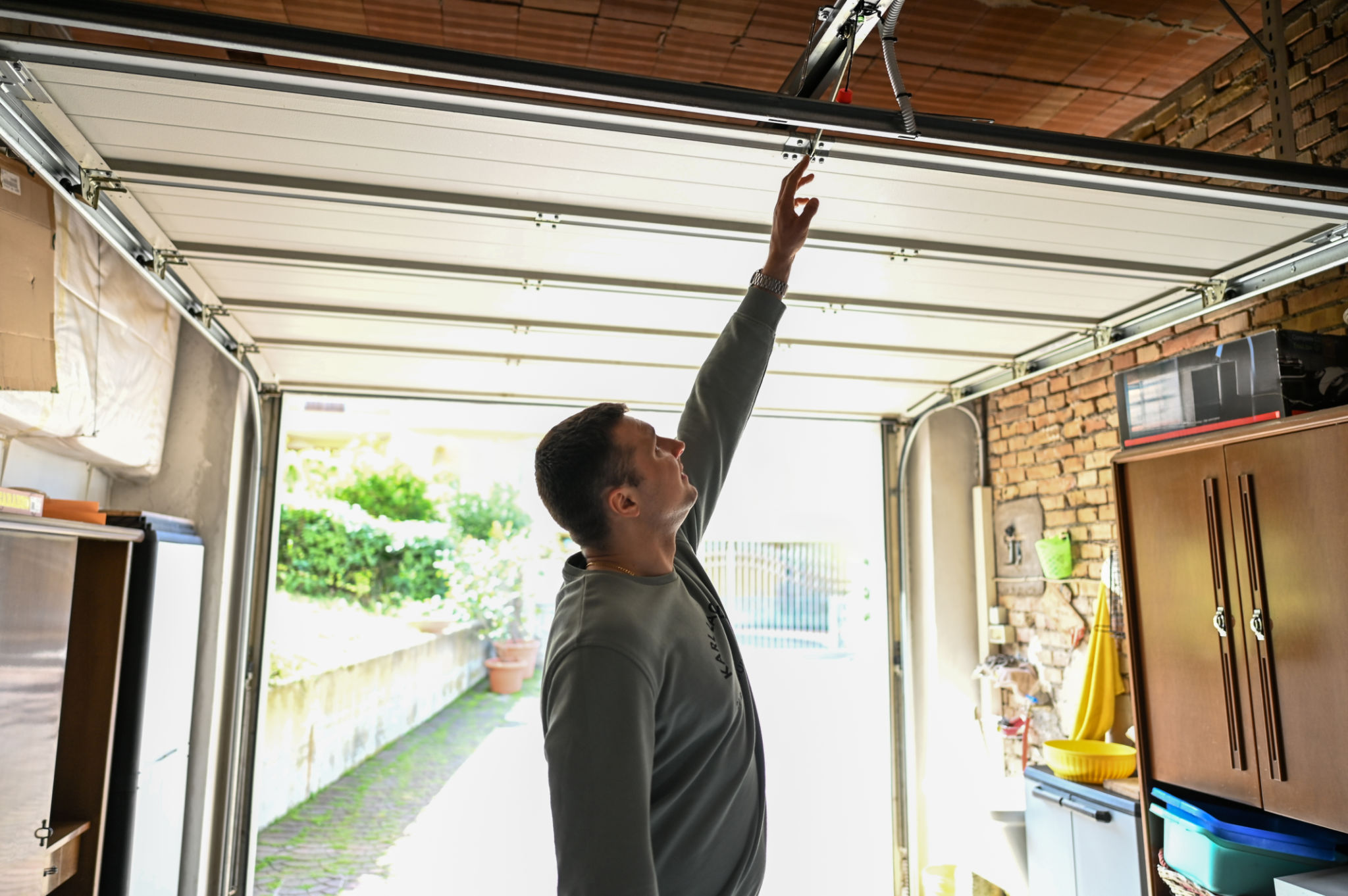
Training and Competency
Ensuring that all employees operating vehicle lifts are adequately trained is another crucial aspect of regulatory compliance. Training should cover the correct use of the equipment, safety protocols, emergency procedures, and an understanding of the relevant regulations. Refresher courses should be provided regularly to keep skills up to date.
Employers should assess the competency of their staff continually, ensuring they have both the knowledge and experience required to operate vehicle lifts safely. Documentation of training programs and competency assessments can help demonstrate compliance during inspections or audits.
Conclusion: Staying Compliant
Compliance with vehicle lift regulations in Lincolnshire requires a proactive approach, incorporating regular training, thorough maintenance, and comprehensive inspections. By adhering to PUWER and LOLER guidelines, businesses can ensure the safety of their operations while protecting their employees and customers.
Understanding and implementing these regulations not only helps avoid legal repercussions but also enhances the reputation of the business as a responsible service provider committed to safety and quality. For any business working with vehicle lifts, staying informed about regulation changes and updates is crucial for ongoing compliance.